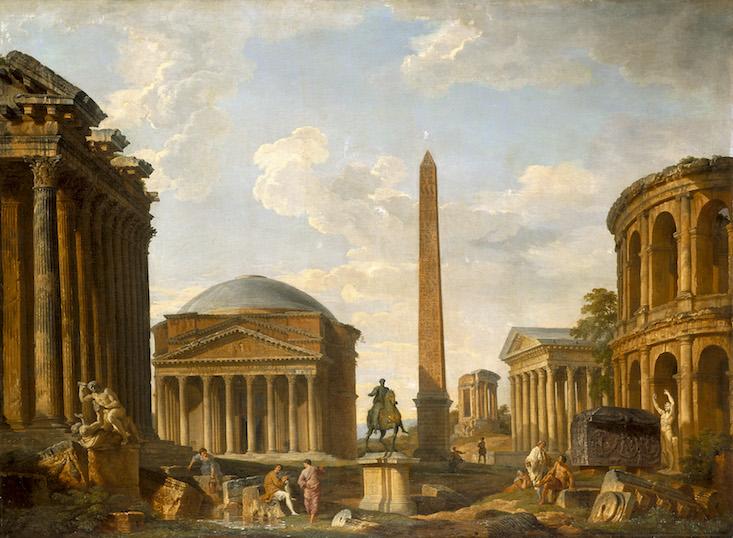
The Roman naturalist Pliny the Elder can be charmingly self-deprecating. He attempted, in the 1st century A.D., to curate all ancient knowledge in his Natural History, yet he described its 37 volumes to his close friend’s son, Titus, the Emperor of Rome, as having “such inferior importance.” To Pliny, they did “not admit of the display of genius,” nor “of anything particularly pleasant in the narration, or agreeable to the reader.” But he reminded Titus of his basic challenge—that it was, “indeed, no easy task to give novelty to what is old, and authority to what is new.”
He might be pleased, then, to see an ancient technology that he himself admired taking on a modern relevance and novelty. Who, Pliny wondered, could help but be surprised at the way the Roman harbor infrastructure, made from a mix of lime and volcanic ash, overcomes entropy, “forming a barrier against the waves of the sea, becoming changed into stone the moment of its immersion, and increasing in hardness from day to day—more particularly when mixed with the cement of Cumae,” an ancient city in Naples?
The geologist and geophysicist Marie Jackson, of the University of Utah in Salt Lake City, shares Pliny’s admiration for these still-standing structures, and has scoured ancient Roman texts in hopes of uncovering the recipe that makes them so durable. The goal would be to revive Roman concrete, and their building techniques, for the modern age—but, alas, her efforts were to no avail.
We have a lot to relearn from the ancients.
So she’s been working backwards. In “Unlocking the secrets of Al-tobermorite in Roman seawater concrete,” a study she and her colleagues published in 2013, they confirmed, via trace element analyses at the Advanced Light Source, an X-ray synchrotron at the Lawrence Berkeley National Laboratory in California, that drill cores of a 2000-year-old block submerged in the Bay of Pozzuoli near Naples came “from Flegrean Fields volcanic district, as described in ancient Roman texts.” The samples contained aluminum tobermorite, a rare mineral and not an ingredient in conventional concrete, which accounted for their great durability and strength. In another study published this month, the researchers found that the aluminum tobermorite grew out of a silicate mineral common to volcanic ash, called phillipsite, spurred by ocean contact. “We’re looking at a system that thrives in open chemical exchange with seawater,” Jackson said.
The tobermorite’s long plate-like crystals grant the concrete an unusual flexibility under stress that increases with time submerged. “It’s a very rare occurrence in nature,” Jackson said. By contrast, modern concrete, made from a mix of Portland cement and coarse aggregate, corrodes in seawater within decades, making the application of Roman concrete, Jackson noted, an enticing option for steel reinforcement-free seawalls that guard against rising sea levels.
Nele De Belie, a materials engineer at Ghent University in Belgium, agrees, and sees fly ash—a product of coal-burning similar to volcanic ash but much more abundant—as the key to inventing new forms of concrete with the sort of “self-healing” properties Roman concrete possesses. Investors are taking notice.
In a recent blog post, Trebuchet Capital Partners, a private equity real estate firm in Los Angeles, states that Portland cement, the world’s standard, is popular because it can be “poured on site” and it’s “cheap to produce.” But architectural projects using fly ash-based concrete will be more sustainable—environmentally, structurally, and economically. The E.P.A. concurs. Using fly ash, the agency’s website states, “can produce positive environmental, economic and performance benefits such as reduced virgin resources, lower greenhouse gas emissions, reduced cost of coal ash disposal, and improved strength and durability of materials.” (It’s not clear if it’s specifically Jackson’s research that’s informing these views.)
“We are entering a new gilded age.”
Since Portland cement production accounts for over 5 percent of human greenhouse gas emissions, in the future, governments might impose a carbon tax on its use. Trebuchet argues that that burden “may be a game changer” for future fly ash use, especially if developers start relying more on automation and 3D printing in concrete manufacturing. Fly ash naturally lends itself better to a manufacturing setting than Portland cement. Developers, Trebuchet predicts, will be able “to make spectacularly detailed molds to form precast friezes and architectural elements…cheaper, faster, [and] with better working conditions.”
What this means, at least for investors interested in building and architecture, is that “we are entering a new gilded age.” People, Trebuchet argues, will stop having “to put up with cookie cutter bland disposable architecture,” and there may even be “a return on [investment for] more superfluous and pretty structures in the neo-classical or Beaux Arts style,” inspired by buildings like the Pantheon.
That’s an outcome that might appeal to the Pantheon-lover John Oschsendorf, a professor of engineering at M.I.T. and a MacArthur “Genius” Fellow who, like Jackson, thinks we have a lot to relearn from the ancients. In his Nautilus Ingenious interview, he told us, “I think the Pantheon is probably the greatest building of all time.” It’s not mere nostalgia. “I’m in awe,” he said, it’s “like a great work of Mozart.” Much of that appreciation stems not just from its aesthetic, but from the fact that we still don’t understand how the Romans did it. That mystery goes beyond construction materials, and into design.
“What we can find are relationships—geometrical relationships—that are encoded within the buildings, which show some of the rules that the builders had,” Oschsendorf told us. “[M]any Roman domes have a supporting wall which is about one-seventh of the span of the dome, and that meant that the builders… were able to devise ratios and proportions that were stable” and “largely independent of scale. Unfortunately, in the Industrial Revolution, a lot of this knowledge was lost. In particular, we don’t often build arches or domes today. It’s very common if you tried to build a structure in [concrete] or brick today that the building code and the engineers involved will insist that it requires steel.”
This highlights the knowledge gap in modern civil engineering, Oschsendorf says. “We’ve lost centuries of knowledge, which has been replaced by other knowledge about how to build in steel and concrete. But today’s knowledge doesn’t necessarily map easily onto those older structures. And if we try to make them conform to our theories, it’s very easy to say that these older structures don’t work. It’s a curious concept for an engineer to come along to a building that’s been standing for 500 years and to say this building is not safe.” The tendency derives in part from a “progress ideology of engineering,” he says, “Something old doesn’t have value to us as a profession. Something new, something hi-tech has value.”
Pliny’s challenge, in composing his Natural History, was giving “novelty to what is old, and authority to what is new.” Modern engineering’s is to see that what is old has some authority, too.
Brian Gallagher is an associate editor at Nautilus. Follow him on Twitter @bsgallagher.